Three demo cases + deep study on quality implication
Global project evaluations supported by LCC and LCA analysis
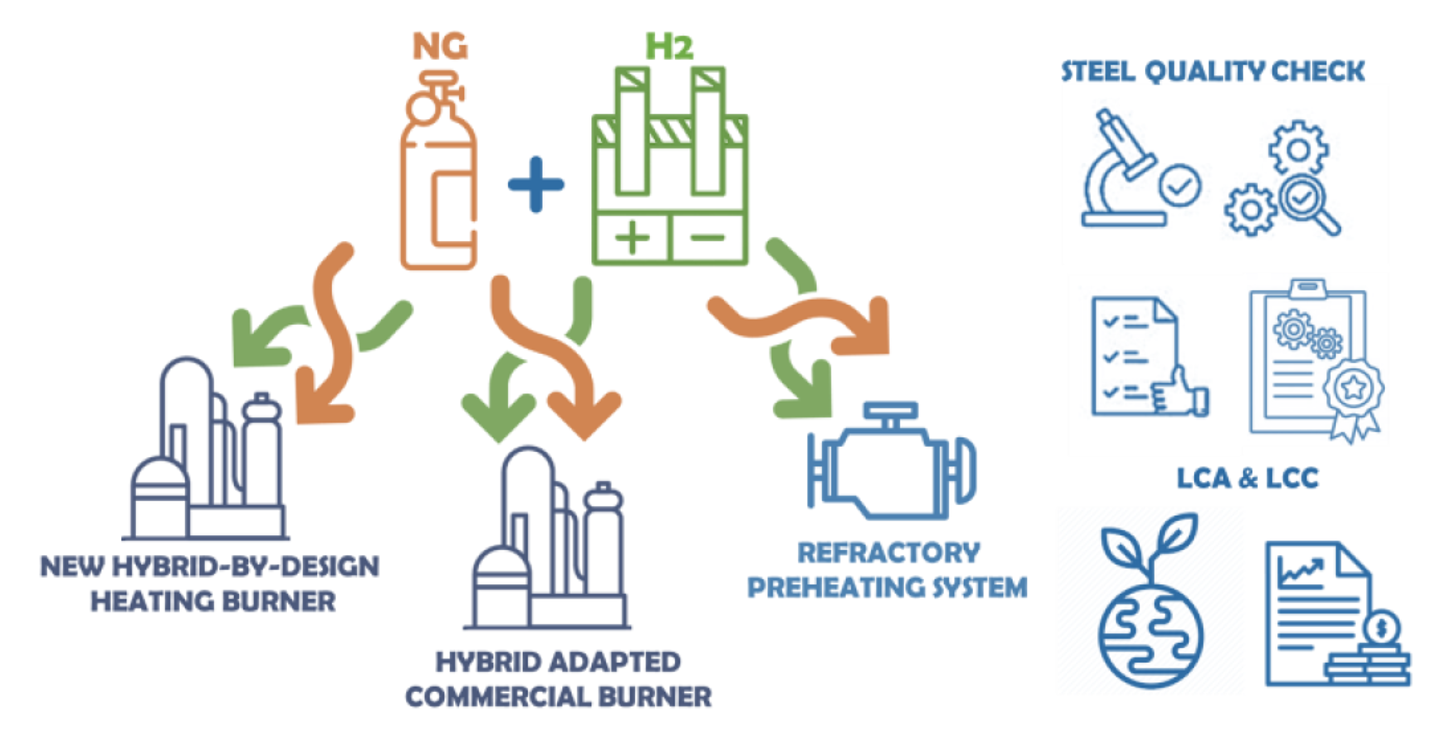
HyTecHeat aims at adopting hybrid heating technology (based on NG with progressive and increasing H2 utilization) in downstream processes so to path the way for the abatement of CO2 for the whole downstream processes
To have a complete picture of the possibility of hybrid technology 3 different democases are envisioned: first in TENOVA democase a hybrid by-design burner will be designed and test in order to evaluate advantage and possible risk needed to be mitigated in this new systems; in TATA democase, a burner currently fully-NG will be adapted to evaluate the limit up to which the current systems can be pushed to work in hybrid heating gas atmospheres without reducing system performance. Finally, in the Nunki democase the effect of hybrid heating system will be evaluated on the quality of the refractory in pre-heating systems.
DEMONSTRATOR 1: TENOVA HYBRID HEATING IN COMBUSTION SYSTEM AT TRL 7
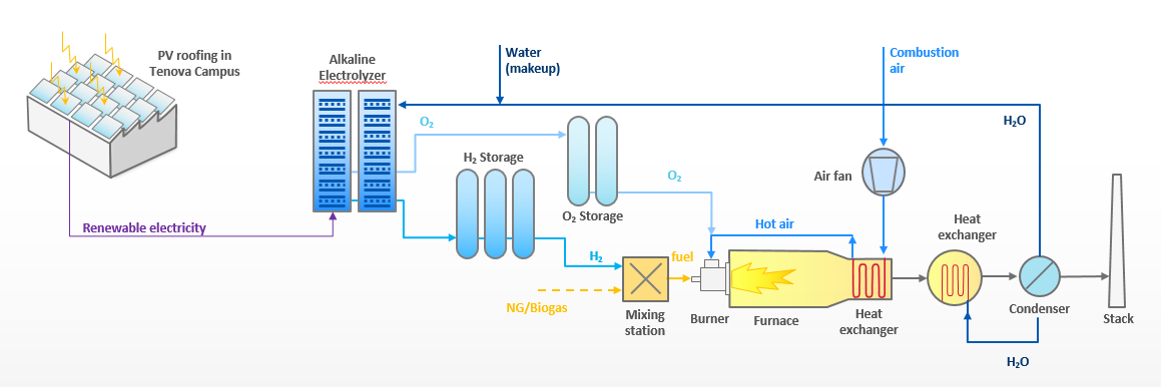
The hydrogen from the vessels is expanded at about 0.3 bar and then fed to the hybrid H2/NG burner prototype (350 kW) that is installed on the test furnace, able to work in real industrial conditions. A combustion control system is installed on a PLC that exchanges control and safety signals with the PLC of the electrolyser and the pressure loop of the hydrogen buffer
DEMONSTRATOR 2: TATA HYBRID HEATING COMBUSTION SYSTEM AT TRL 7 -
TATA aims to test the currently employed burners in its site with a mixture of hydrogen and natural gas. The burners to be tested are normally optimized for natural gas.
The tests will be carried out in the pilot furnace in the facilities of TATA. The installation is a horizontal cylindrical furnace of 1300 mm inner diameter and 3500 mm inner length. The furnace can withstand 1400 °C and it can accommodate industrial burners up to 500 kW capacity.
The test furnace is equipped with a pre-combustor to preheat combustion air. This precombustor consists of a burner connected to a combustion chamber in which required combustion air for the burner to be tested is preheated.
Using the existing burners also brings immense benefits that can be achieved quickly and with limited CAPEX.
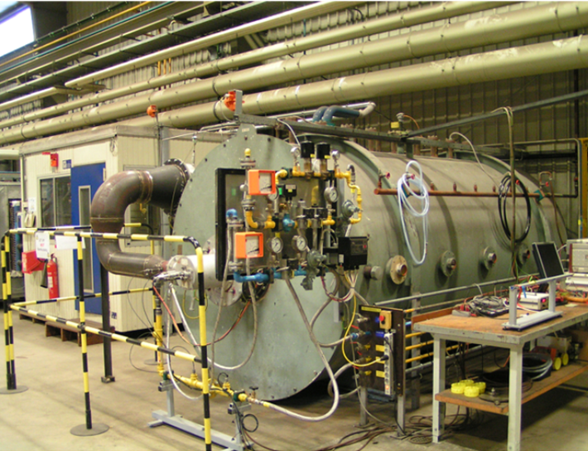
DEMONSTRATOR 3: Nunki HYBRID HEATING PRE-HEATING REFRACTORY SYSTEM AT TRL 7
Nunki will test the possibility to use H2 / NG blends for ladle refractory preheating. A preliminary activity of testing of burners has already carried out by Rina-CSM confirming the suitability of the burner to work with H2 / NG blends.
The burner has 2 MW maximum power, (the working range is between 0.2 MW ÷ 2 MW). Different blend compositions will be tested (maximum value of 60%).
Safety issues will be considered and solved for the demonstrator 3 realization. This will occur, since Hydrogen would be employed as combustible in an industrial area not yet designed for this purpose.
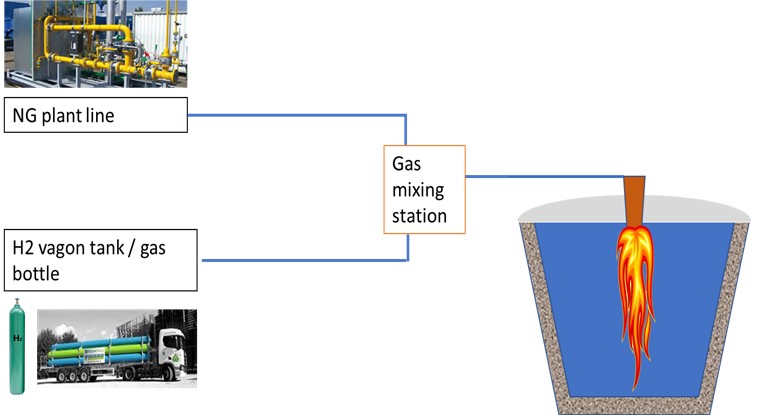
STEEL QUALITY EVALUATION: THE BRIDGE TO TRL 8
The assessment of the relationship among thermal gradient, steel grades and composition of combustion atmosphere on the formation of scale, effects on surface quality and scale removal will be carried out with purposely designed experimental activity. This assessment requires thermogravimetric tests (for determination of oxidation kinetic), descaling tests (for scale removal characterization) and thermal treatment on larger steel samples to simulate scale in an environment closer to the industrial one.
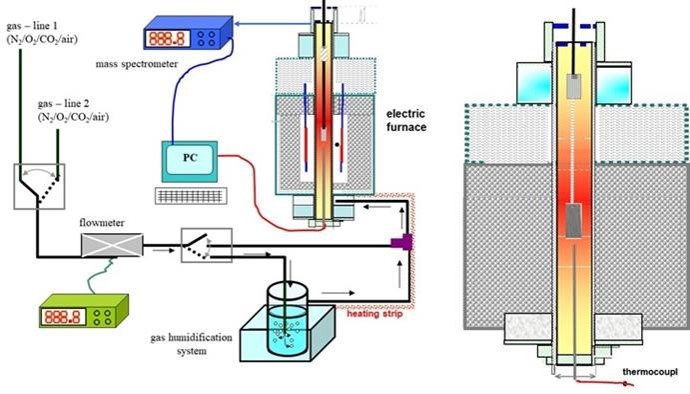
Laboratory: TGA - Thermogravimetric tests
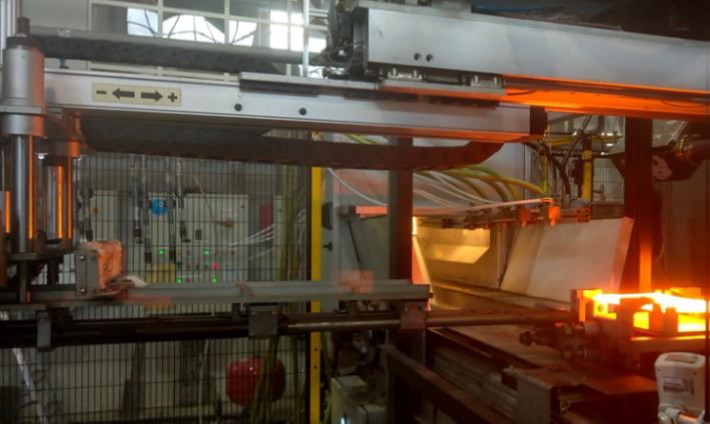
Pilot plant: descaling tests
Another important aspect is the scale removal. A scale formed in a steam atmosphere tends to be more ductile and adherent. To study these effects for different steel grades (carbon and stainless steels) a burner for the pilot descaling furnace will be purposely adapted to work with blends hydrogen/natural gas. The effect of H2 addition to the combustible mix will allow to verify the positive or negative variation respect the standard setting of the descaling unit. Test will also be performed with advance descaling technology to evaluate the beneficial effect of the precooling and/or double nozzle; the tests will be performed in condition close the critical values od descaling ability. The metallographic analysis is necessary to confirm the results from visual aspect also at high magnification in cross-section. In the descaling tests steel samples will be exposed to combustion atmospheres. The condition of the pilot descaling unit o will be according with the industrial process (same reheating conditions) for: heating type, nozzle types, different descaling parameter settings which result in different Impact pressures, specific water impingements and descaling energies. The descaling trials will be performed at RINA-CSM, SWERIM and AMMR facilities.
Tenova will supply an air burner for a prototype test in the 3-400 kW range and will provide installation assistance and expertise. Linde will support expertise for the operation of the oxyfuel burner. SSAB will provide expertise on material benchmark behaviour, deliver material and analyse the results in their material laboratory.
The subsequent material investigations will provide insights into the material response in decarburization depth, oxide thickness and quality of descaling.